Apr 11, 2025
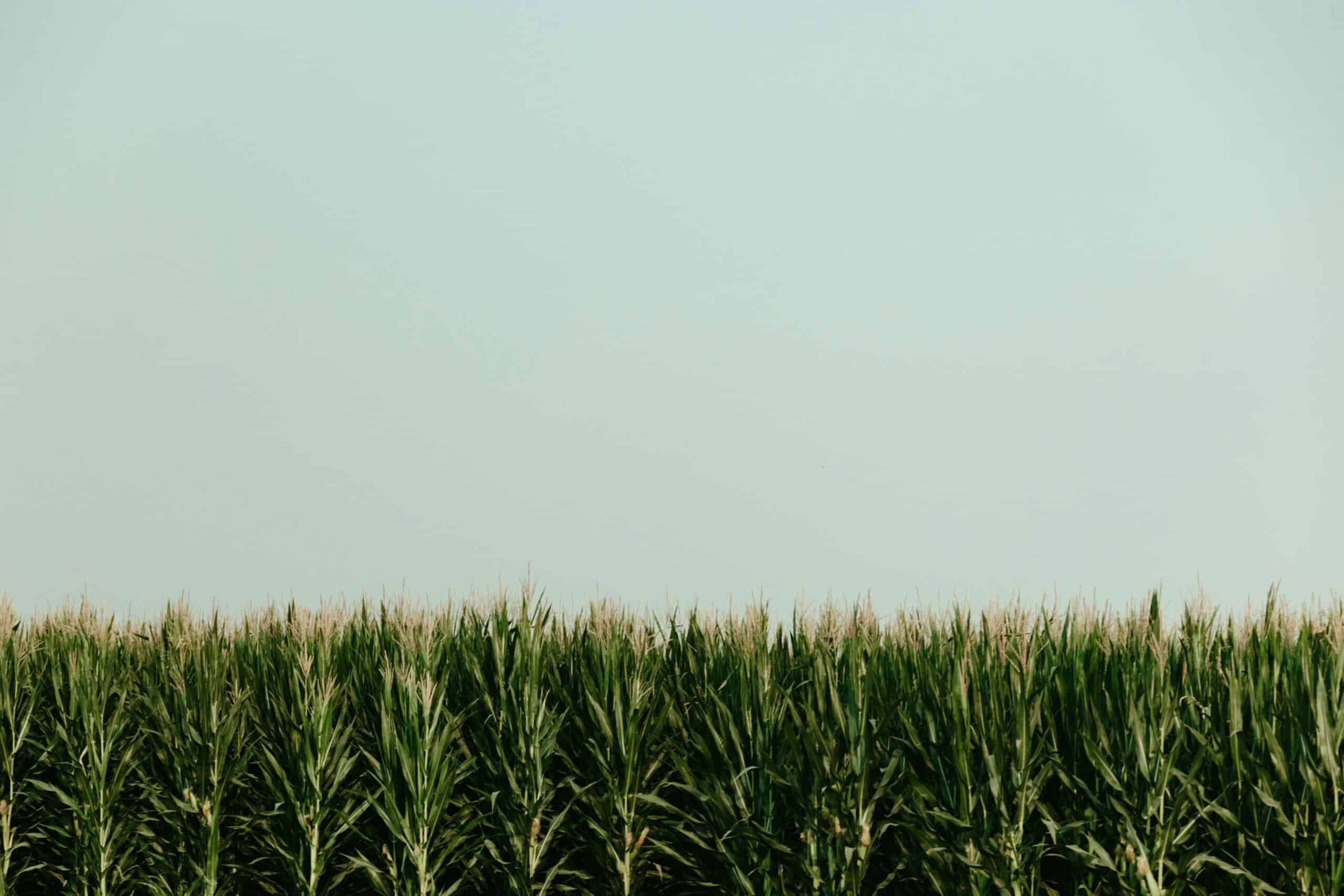
If you could do something twice as fast in your fields as you normally do, with the same results, you would do it, right? What about three times faster?
What if, by doing something more efficiently, you could also improve the overall results? Well, believe it or not, it’s possible.
Tank mixing agricultural inputs, including biologicals, can save time and be economical. You can spray your fields more efficiently and potentially improve product efficacy by tank-mixing agricultural products.
Don’t run to your sprayer just yet! If done wrong, the results can range from disappointing to disastrous. Whether an incompatible mix clogs your machinery or causes crop injury due to chemical incompatibility, tank-mixing with products new to your operation requires correct handling and attention to mixing instructions. Attention to detail is crucial to reaping the benefits that can positively or negatively impact yield.
Here are the basic principles of tank-mixing every grower should know to ensure a successful tank mix and application.
Tank-mixing is when a grower mixes multiple agricultural inputs into a single tank to make a single spray application for his/her fields. This allows the grower to treat various stressors, manage fertility, or enhance the efficacy of other products in a single pass.
Mixing multiple products together in one tank could include a combination of products like pesticides, fertilizers, macro-micronutrients, soil microbial foods, biostimulants, plant growth regulators, and adjuvants.
Suspension: a mixture of fluid and solid particles
Carrier: primary material, such as water or fertilizer, used to allow pesticides, herbicides, fungicides, etc., to be dispersed effectively
Adjuvant: a performance-enhancing substance added to the crop input spray mix
Agitate: stirring or shaking the tank
Agricultural products commonly found in a tank mix include:
Growers normally use water or fertilizer as the main carrier of the tank mix to combine solutions together.
It’s important to know the water and other value-added products’ pH level, mineral content, and temperature to avoid creating a compatibility issue. A proper pH level and temperature are needed for the products to mix and dissolve efficiently. When mixing with living biologicals, pH can impact when these products become active and release their active ingredient, and pH can have an impact on the viability of these organisms. For best practice, follow manufacturing instructions to know what pH is needed when adding living biologicals.
The mineral levels can compromise applications by mineral bonding. High levels of calcium, aluminum, iron, magnesium, chlorine, and sodium in hard water can have a negative impact on herbicide, pesticide, and biological performance or inhibit the compatibility of the products.
When mixing any products with fertilizer as the carrier – rather than water – keep an eye on pH levels due to these products having very high or low pH levels. Many products, like biologicals, require pH stabilization before mixing with other agricultural inputs.
The type of formulation, e.g., powder, liquid, etc., of each product determines the mixing order of each product into the carrier. Here are some of the most common formulation types.
Abbreviation | Name | Notes |
DF | Dry Flowables | Clumps are more easily broken up and recovered than WP |
EC | Emulsified Concentration | Phytotoxicity risk |
EW | Emulsion in Water | |
F | Flowable Liquid | |
ME | Micro-encapsulated | |
OD | Oil Dispersion | |
S | Solution | |
SC | Suspended Concentrates | Easiest to apply Lowest callenge risk |
SG | Soluble Granule | |
SL | Soluble Liquids | Easiest to apply Lowest callenge risk |
SP | Soluble Powder | |
WDG | Water Dispersible Granule | |
WSP | Water Soluble Packet | |
WP | Wettable Powder | Creates the greatest challenge due to clumping |
To know which products to apply first, refer to the W.A.L.E.S. acronym described later in this blog post.
When it comes to tank-mixing, the wide range of benefits far outweighs the risks, especially since risks can be avoided. From cost-savings to improved efficacy, tank-mixing benefits both growers and crop performance.
From pesticides to fungicides, tank-mixing can support your crops by targeting pests lurking in your fields. A grower can use a complex tank mix to target multiple biotic and abiotic stressors in one treatment, rather than relying on multiple treatments and field passes – improving overall crop performance and implementing more sustainable agricultural practices. It’s also an easy way to improve your resistance management from different angles and take out hard-to-kill pests.
Tank-mixing agricultural inputs gives a grower labor and fuel cost savings. It decreases the cost of application by reducing total passes in a growing season. By driving heavy machinery in your field less frequently, you are able to minimize crop damage and reduce soil compaction. Efficiency saves growers money and adds to the bottom line!
When mixed, some agricultural products create synergy. This means the inputs provide better results when applied together rather than alone. Spray adjuvants, for example, can enhance the efficacy of active ingredients.
Heavy machinery passes contribute to soil compaction, which damages your soil’s microbiome – an ecosystem that supports crops when activated. Tank-mixing helps growers reduce the number of passes in a field by applying a more diversified treatment with a single pass, mitigating compaction damage.
Mixing agricultural products is good for growers because each grower can apply a timely application based on weather conditions, crop stage, or pest life cycle.
Tank-mixing mistakes can result in compatibility issues that impact how a product is dispersed, mixed, and delivered, which may negatively impact the product’s overall performance in the field. Each product has a set of complex chemical structures. When new agricultural products are added to your tank, the likelihood of a compatibility issue arising increases.
These mistakes can occur when combining inputs or by not taking the proper steps when evaluating new tank-mix partners.
An input mistake could look like:
Most of these problems can be avoided by reading the label and adhering to restrictions or best practices when mixing multiple products. Always examine a label closely to avoid damaging your crops or machinery.
A mixing mistake could look like:
There are two kinds of incompatibilities that can result from input or mixing mistakes: physical incompatibilities and chemical incompatibilities.
Physical incompatibilities occur when products or ingredients do not mix properly, which can block the spray systems and disrupt application. Signs you may have a physical incompatibility include:
Chemical incompatibilities occur when the spray mixes and looks fine in the tank or jar test, but the mixed products are chemically incompatible. Just because a mix looks fine doesn’t mean it is.
Sometimes, a chemical incompatibility reduces biological activity or efficacy. Other times, a chemical incompatibility can injure or kill crops. It can take hours or even days to notice if a chemical incompatibility has taken place after an application.
If you discover there is a physical or chemical incompatibility in your mixture, all gels and solids must be flushed from tanks, filters, screens, and nozzles. Consult with a chemical company representative or agronomist before dumping an incompatible mix.
The time lost, and cleanup can be expensive, and the materials can be difficult to dispose of. Work with a professional to ensure it’s done right. Otherwise, you could make a bad situation worse.
A little extra planning and testing can go a long way. Interested in spraying a new agricultural input in your field? Consider doing a jar test to ensure there are no unforeseen reactions.
A jar test provides the grower with the ability to test the same level of concentration as their tank mix. While jar tests are a great choice to check for physical incompatibilities, they cannot reveal chemical incompatibilities, so conduct a spray test too, if needed.
The things you’ll need for a jar test include:
Place inputs in the jar in the appropriate ratios and order depending on the desired tank application. Then, cap the jar and shake well. Leave the jar for at least two hours, but preferably overnight.
Signs of physical incompatibilities include flocculation, precipitation, curdling, gelling, or formation of a sludge-like mix. Settling of flowable or powder products is normal.
Note: If it’s hard to resuspend sediments, extra agitation during spraying may be needed to avoid blockage or uneven application. If the mixture appears to be incompatible (see signs above), take steps to improve compatibility by adding a compatibility agent, evaluating the mixing order, or adding additional water.
A jar test can help ensure you don’t clog your sprayer. If there are no formulation or physical incompatibilities once the chemicals are mixed, check for chemical incompatibilities. Then, mix in the tank and spray!
First, read the labels and check the quality of your carrier beforehand to establish a baseline for pH, hardness, bicarbonate, salinity, or total dissolved salts.
Once you know the amounts and order of products you’ll be mixing in the tank, fill the tank half full of water or 3⁄4 full of fertilizer, depending on your desired carrier. Never add agricultural products to an empty tank.
Agitate all the product you will be using before adding them into the tank mix. Agitation can help achieve a more even application in your fields.
Then, agitate the carrier in your tank and begin adding the agricultural inputs. Use the acronym W.A.L.E.S when adding products to the tank.
W: Wettable powders or dry formulations (WP/W, WDG, WSP, or DF)
A: Agitate the mix until the powders are fully dissolved
L: Liquid flowables (L, F, SC)
E: Emulsifiable concentrates (EC, then ME)
S: Surfactants and other adjuvants
Allow adequate time for each product to mix. Once all the products are in, finish filling the tank with your carrier. Test the pH to make sure everything is safe for application.
Then, head out into the fields to apply the tank mix to your crops.
Inside your soil is a microbiome, or community of microorganisms. Unfortunately, 75% of all beneficial microbes in farm soil are either dormant, unhealthy, or starving. When active, native microbes can support your crop throughout the growing season. How?
An active and well-fed microbiome:
PhycoTerra is a pasteurized, shelf-stable, carbon microbial food source with minimal storage requirements. It can be applied to any type of soil to promote the well-being of any type of crop.
You can mix PhycoTerra with liquid fertilizers, like nitrogen, phosphate starter or pop-up fertilizers, fertilizer blend partners, and specialty fertilizers. Activated microbes help make the most of your fertilizer application!
Our product can also be mixed with fertilizer blend partners, like enzymes, inoculants, seaweeds, kelps, humic acids, and other living biological products. Stacking carbon products is a smart decision for any field.
Common crop inputs, like herbicides, fungicides, and insecticides are also easily applied and mixed with PhycoTerra.
This carbon-rich product is a smart way to make the most of any tank mix.
The hardest part about adding biologicals to your tank mix – they’re alive. They also need to stay alive to support your crops. Follow the best practices to keep microbes and inoculum alive before, during, and after you spray.
Improper storage, on your farm or in transportation, can kill your microbes or inoculants before they have a chance to enter your spray tank.
Once at your farm, keep-in-mind direct sunlight and heat can kill inoculants or live biological products. Store in a cool place out of the sun. The preferred storage to protect inoculants is in a cool, dry place. Most of these products also require specific storage that doesn’t expose them to freezing temperatures.
Also, always check the expiration date! If you’re not sure if your biologicals are alive or not, have a lab measure the agricultural product for colony-forming unit counts (CFU).
Bactericides, biocides (like copper and manganese), and treated water can kill microbes and inoculants in your tank.
Don’t mix biologicals with competing microbes, which could consume one another. Some competing microbes can be applied in the same tank if they’re sprayed within two to four hours of mixing.
Due to lower concentrations when sprayed, the organisms won’t feed off one another once sprayed.
Some agricultural products will require you to neutralize the pH before tank-mixing with other living biologicals or inoculants. You can determine if neutralization is needed by reading the labels of each product before tank-mixing.
For example, when using PhycoTerra ST, we suggest growers mix our award-winning seed treatment with potassium hydroxide – 45% (KOH) – if applied with biologicals that are sensitive to low pH levels. Growers should add a 5.65 liquid oz. of KOH with a full jug (2.5 gal) of PhycoTerra ST. When mixing with KOH, follow all safety precautions on the label.
Mix the two together, either with a stir stick or a power drill with a paint mixer attachment. Then, allow the jug to settle and wait 2 minutes for the stabilizer to neutralize the pH to protect biologicals.
Read the full instructions here.
If you can, spray your biologicals with nutritional treatment products for your crops. Often, what feeds the plants also feeds the microbes.
If you’re going to mix with fertilizers, avoid synthetics with a high-level electric conductivity (EC).
Once you’re ready to spray, pick a biological safe nozzle spray level. Biologicals can be sprayed safely at a 65 psi nozzle pressure, or lower, to protect microbes.
Accidents happen but running through this list of questions can decrease your chance of accidents and incompatibilities.
While there are Mix Tank Apps growers can use to tank mix agricultural inputs, the more you know about the products you’re putting into your sprayer, the better your odds of avoiding a frustrating situation or disaster.
Knowing the answers to the questions above can ensure you’re making the most of your time and money when it’s spray day. Revisit the questions each time you plan to tank mix.
Ready to add a soil microbial food to your tank mix? Reach out to learn how PhycoTerra can support the health of your soil, ROI, and yield potential.
Preserving the Future of Farming
Learn more about our mission to keep farming economically and ecologically sustainable.
Learn MoreJoin our mailing list to learn more and receive special promotions.
© 2025 Heliae Development, LLC DBA PhycoTerra®.
All Rights Reserved. | Sitemap